Сверхзвуковой струйно-форсуночный аппарат (СФА)
1. Введение.
Инжекторами или струйными аппаратами называются устройства, в которых осуществляется процесс инжекции, т.е. передача кинетической энергии от одного потока другому путем непосредственного контакта (смешения) потоков. Смешиваемые потоки могут находиться в одной и той же фазе (жидкой, газовой, паровой) или в разных фазах (пар и жидкость, газ и твердое тело и др.). В процессе смешения фазовое состояние смешиваемых потоков может оставаться неизменным или же изменяться (например, пар может конденсироваться в жидкость). Поток вступающий в процесс смешения с большей скоростью называется рабочим, с меньшей — инжектируемым. На рис.1 показана наиболее общая схема струйного аппарата.
Рис.1 Схема струйного аппарата: А — рабочее сопло; В — приемная камера; С — камера смешения; D — диффузор. Где: Gн, Рн, Wн, Iн — соответственно расход, давление, скорость, энтальпия инжектируемого потока; Gр, Рр, Wр, Iр — то же для рабочего потока; Gc, Рс, Wс, Iс — то же для потока смеси; 1 — 1 — входное сечение камеры смешения (КС); 2 — 2 — выходное сечение КС. |
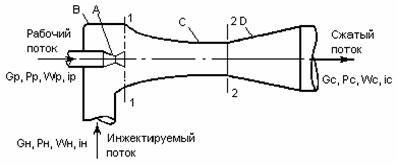 |
Общий принцип действия такого аппарата: потоки рабочей и инжектируемой сред поступают в камеру смешения (КС), где происходит выравнивание скоростей, сопровождающееся повышением давления. Из КС поток поступает в диффузор, где происходит дальнейший рост давления. Давление смешанного потока на выходе из диффузора выше давления инжектируемого потока, поступающего в приемную камеру, но ниже давления рабочего потока, т.е. Рн<Рс<Рр. Однако, необходимо отметить, что не у всех струйных аппаратов сжатие инжектируемого потока происходит непрерывным образом. Действительно, по уравнению неразрывности струи, скорость несжимаемого потока должна уменьшатся по ходу течения, вдоль непрерывно расширяющегося канала (в диффузоре), что сопровождается плавным ростом статического давления согласно уравнению Бернулли. Непрерывный рост давления смеси имеет место также из-за торможения потока в канале постоянного или переменного сечения за счет сил вязкостного трения. Но для сжимаемого потока, каким является однородная, мелкодисперсная газо или парожидкостная смесь, имеет место скачкообразный переход части кинетической энергии в потенциальную энергию статического давления, причем такой переход наиболее эффективен в канале постоянного сечения. Дальнейшее повышение давления смеси в диффузоре может вносить даже существенно меньший вклад в рост давления. Мы будем применять термин струйный аппарат в более широком смысле чем инжектор, так как механизм получения однородной двухфазной смеси не обязательно должен сводится к взаимодействию однонаправленных потоков движущихся с разными скоростями. Такая смесь может образовываться, например путем насыщения потока жидкости газом или паром из трубок с множеством мелких отверстий (барботирование). Важно, при торможении газо или парожидкостной смеси, полученной каким-то образом, указанное скачкообразное повышение давления имеет место. Причем среди таких струйных аппаратов существует класс аппаратов, у которых давление смешанного потока может превышать не только давление инжектируемого потока (жидкости), но и давление рабочего потока (пара или газа), т.е. не только Рс>Рн, но и Рс>Рр. Пароводяной струйный аппарат или пароводяной инжектор (ПВИ) был известен достаточно давно, так патент на него был получен французским инженером Жиффаром еще в 1858г. Предполагалось, что значение давления парожидкостной смеси Рс на выходе из него должно быть как у других инжекторов: Рр>Рс>Рн. Однако, хотя такой результат и согласовывался с существующей в то время теорией расчета, на практике наблюдалось, что при определенном сочетании геометрии проточной части и параметров потоков на входах в аппарат, на выходе значение давления могло получать скачок, существенно превышающий давления входных потоков. Такие “скачковые” аппараты оказались интересными тем, что паровая фаза полностью конденсируется не только в результате теплообмена между фазами, но и в скачке давления совпадающем с окончательной конденсацией паровой фазы (скачок конденсации). В пароводяном струйном аппарате реализуется однородное, мелкодисперсное смешение паровой и жидкой фазы на относительно небольшой длине. Затем паровая фаза окончательно конденсируется, выделяя содержащуюся в ней теплоту. Таким образом, имеем высокоэффективный теплообменник смесительного типа у которого температуры холодной и горячей компонент выравниваются в потоке смеси за короткий промежуток времени. На выходе получаем нагретую однофазную жидкость под давлением, без использования электроэнергии на работу насоса, при этом сам аппарат может быть очень компактным (<1м) по сравнению с традиционным пароводяным кожухотрубчатым теплообменником (бойлером), а следовательно, теплопотери с площади поверхности пренебрежимо малы. Важно отметить что, говоря об энергоэффективности аппарата, мы имеем в виду не эффективность преобразования кинетической энергии рабочего потока (пара) в кинетическую энергию разгоняемого инжектируемого потока (воды) с последующим переходом в потенциальную энергию сжатия потока смеси. Эта эффективность достаточна мала из-за больших потерь кинетической энергии в виде переходов в тепловую энергию. Однако с точки зрения рассматриваемой нами задачи: получить на выходе аппарата горячую воду с требуемой температурой и давлением, имеем преобразование суммарной тепловой и механической энергии потоков на входах в аппарат, в необходимую нам тепловую и механическую энергию смеси на выходе практически без потерь. Потерями этом случае будет рассеивание тепловой энергии в окружающую среду, которые для данного аппарата пренебрежимо малы. Так у бойлера холодная вода получает тепловую энергию от пара, находящегося в межтрубном пространстве, его трубки, особенно при жесткой воде, достаточно быстро покрываются накипью, теплопроводность которой в 40 с лишним раз меньше теплопроводности стали. Тогда на выходе теплообменника мы получаем конденсат не охладившийся до температуры нагреваемой им воды, а иногда даже не до конца сконденсировавшийся пар. Тепловая энергия, отданная паром нагреваемой воде и окружающей среде, представляет собой разность энтальпий соответственно пара на входе и конденсата на выходе из бойлера. Очевидно, что эта разность существенно уменьшается при неполной конденсации. При применении же струйного аппарата, пар поступающий на его вход, преобразуется полностью на выходе в конденсат, причем с температурой равной заданной температуре смеси, что позволяет существенно увеличить передачу от пара тепловой энергии и соответственно снизить его расход. Будем называть указанный класс аппаратов СФА (сверхзвуковой струйно-форсуночный аппарат). Основанием для такого названия является тот факт, что возмущение параметров на выходе аппарата (изменение противодавления) не меняет параметров на входах, что указывает на наличие сверхзвукового перехода при движении смеси в аппарате и скачка давления как следствие этого перехода. Это дало основание называть подобный класс аппаратов терминами SUPERSONIC INJECTOR (M.A. Grolmes) или TRANSSONIC (В.В. Фисенко). Параметры работы данного аппарата были расширены условием подачи жидкости из напорного трубопровода с некоторым давлением Рн превышающим атмосферное. Таким образом, данный аппарат может работать не только в режиме всасывающего инжектора, создавая разряжение на входе в жидкостный патрубок и подсасывая воду из резервуара, но и с водой под давлением, причем давление двух потоков (пара и воды) на входе в аппарат могут быть примерно равны. При этом необходимо рассчитать такую площадь жидкостного сопла Fжс (рис. 2), чтобы сдросселировать избыточное давление воды.
2. Геометрия проточной части аппарата.
В результате использования теории термо — и гидрогазодинамики двухфазных сред и большой экспериментальной работы, были выявлены наиболее эффективные варианты решений геометрии проточной части аппарата. Она была предложена в виде суживающейся камеры смешения (КС) с постоянным или переменным углом конусности и цилиндрическим горлом диффузора (ГД) (рис.2).
Где: 1 — сопло для ввода пара (сопло Лаваля или сужающееся), 2 — патрубок для подачи жидкости, 3 — жидкостное сопло 4 — нагретая жидкость к потребителю. КС — камера смешения, ГД — горло диффузора. F*п.с.- площадь минимального сечения парового сопла. Fж.с.- площадь жидкостного сопла, Fг.д.- площадь горла диффузора или минимального сечения КС. |
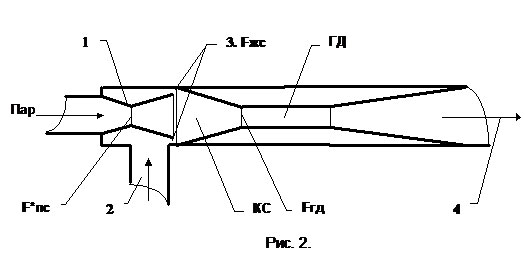 |
Подвод пара осуществляется через сужающееся дозвуковое или сверхзвуковое сопло Лаваля. Выбор сопла определяется отношением давления пара на выходе из сопла и давлением жидкости на входе в аппарат. Это необходимо, чтобы струя пара после выхода из сопла не была недорасширенной или перерасширенной. Жидкостное сопло, предназначенное для использования перепада давления между входом в аппарат и камерой смешения, выполнено в виде кольцевой щели или ряда отверстий между паровым соплом и стенками КС (рис.2). Были выявлены необходимые соотношения геометрических размеров которые давали давление смеси на выходе превышающие давление на входах в аппарат. Для описания геометрии проточной части оказалось эффективной введение величины безразмерной площади горла диффузора Fгд=Fгд/F*пс (F*пс — площадь минимального сечения парового сопла) и безразмерной площади жидкостного сопла Fжс=Fжс/Fгд. Так для аппарата с Fгд=0.077 и Fжс=1.8 при степени расширения парового сопла М =2.44 удалось запустить аппарат при помощи сбросной линии и получить восьмикратное (!) превышение давления смеси на выходе над давлением пара на входе: Рс/Рн 8. Геометрия проточной части описана в общем виде. Расчет внутренних размеров аппарата выполняется специалистами фирмы, исходя из данных по каждому конкретному объекту. Также кроме струйных аппаратов с центральным подводом пара и периферийным подводом жидкости (рис. 3, а) были разработаны методики расчета аппаратов со скачком давления для центрального подвода жидкости и периферийным паровым соплом (рис. 3, б), а также для аппаратов с впрыском жидкости в паровой поток осуществляющийся многоступенчато, начиная с суживающейся части сопла Лаваля (рис. 3, в).
|
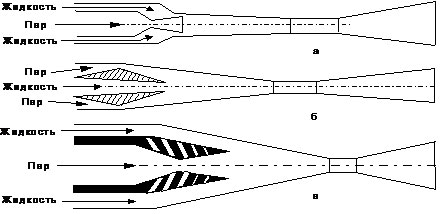
|
|
|
Рис.3 Схемы двухфазных струйных аппаратов. |
|
Выбор той или иной схемы зависит от поставленной задачи. Так основное преимущество схемы с центральным подводом пара в том, что здесь к.п.д. парового сопла при прочих равных условиях имеет наибольшее значение; это особенно важно при работе с паром высокой степени влажности при низких давлениях пара, где к.п.д. парового сопла резко снижается. Схема с центральным подводом жидкой фазы, несмотря на снижение к.п.д. парового сопла, позволяет лучше организовать процессы в КС и снизить потери на стенках КС. Кроме того, для установок с малой производительностью улучшается к.п.д. жидкостного сопла, т.к. в случае периферийной подачи жидкости зазоры для ее прохода могут составлять десятые доли мм. Это особенно важно для аппаратов использующих вязкие жидкости и жидкости имеющие включения в виде загрязняющих примесей. Примеры использования таких жидкостей в парожидкостных струйных аппаратах : • приготовление водотопливной эмульсии из мазута и пара; • приготовление суспензий и т.д. Также необходимо отметить, что центральный подвод жидкости эффективен в случае равенства или превышения давления жидкости на входе в аппарат над давлением пара, в этом случае поток жидкости целесообразно использовать в качестве рабочего потока.
3. Физика процесса.
Оказалось, что неравновесные процессы, происходящие в КС таких аппаратов чрезвычайно сложны, кроме обмена импульсом и теплообменом между паровым потоком и частицами жидкой фазы протекают фазовые переходы. В КС осуществляется дробление и разгон частиц жидкой фазы, а также почти полная конденсация паровой фазы на более холодной жидкости, что приводит к перестройке структуры потока. Если в начальном участке КС движутся разделенные, но взаимодействующие паровая и жидкая фазы, то затем поток приобретает капельную структуру с практически равномерно распределенными по объему каплями. Т.к. струя дробится на мелкие капли, то в результате площадь поверхности теплообмена оказывается очень большой, при этом теплообмен на струе жидкости становится интенсивным. В конце КС, структура потока перестраивается, среда приобретает пенную, тонкопленочную структуру с заполненными паром полостями, которая характеризуется максимальной площадью поверхности контакта фаз. Это соответствует максимальной интенсивности теплообмена, конденсации пара и соответственно возрастанию плотности смеси [1]. При конденсации пара создается разряжение, т.к. конденсат имеет значительно меньший удельный объем. На выходе из КС, когда паровая фаза в основном сконденсировалась, поток через пенную структуру переходит в пузырьковую (пузырьки пара в жидкой среде). Такая среда обладает необычными свойствами, по отношению к скорости распространения звука в ней, что и составляет основу для формирования скачка давления. Рассмотрим историю этого вопроса. В работах к.т.н. Н.Г. Морозова (ВТИ) [2] впервые детально исследовавшего распределение давления по длине проточной части струйных аппаратов при различных режимах работы, еще в 1939-1940г. было предложено объяснение наблюдающегося в диффузоре этих аппаратов скачка давления. Это объяснение основывалось на рассмотрении смеси жидкости с не сконденсировавшимся паром как квазиоднородной эмульсии, к которой приложимы все обычно применяющиеся уравнения движения однородной сжимаемой жидкости, а также понятия о критической скорости, критическом расходе и пр. Н.Г. Морозовым было дано общее уравнение движения такой эмульсии, учитывающее как трение, так и конденсацию (или испарение) и изменение секундной массы струи. Скачок давления в диффузоре объяснялся им как скачок уплотнения, сопровождающий переход от сверхзвуковой скорости струи к дозвуковой с завершением при этом конденсации пара, а величина скачка давления определялась с помощью уравнения количества движения. Основанием для развития теории такого рода аппаратов стали работы по изучению скорости звука в парожидкостных и газожидкостных смесях. Так в работе [3] было теоретически показано, что процесс кавитации (появление в жидкости зародышей паровой фазы) сопровождается резким уменьшением величины скорости звука. В работе [4] были рассчитаны значения скорости звука для разных температур жидкости в насыщенной воде со стороны двухфазной области, при этом было обращено внимание на аномально низкую скорость звука в такой среде. В работе [5] как теоретически, так и экспериментально было показано, что скорость звука в газожидкостной смеси в большой степени зависят от сжимаемости этих компонент. Смесь, состоящая из почти несжимаемой жидкости и сжимаемого газа или пара, имеет более высокую сжимаемость, чем даже у газовой фазы, а потому звуковая скорость в ней ниже, чем просто в газе. Итак, скорость звука в средах аналогично той, что мы имеем на выходе из КС (гомогенная пузырьковая смесь газ — или пар — жидкость) имеет аномально низкое значение скорости звука (рис. 4.1., 4.2.)
|
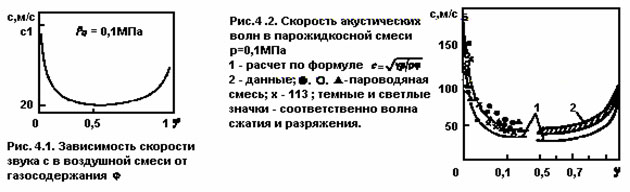
|
|
Значение скорости звука в такой среде может опускаться, например, до 10 м/с (скорость звука просто в паре или в воде соответственно порядка 500 или 1500 м/c). Таким образом, при умеренных скоростях 40 — 50 м/c движения парожидкостного потока мы можем получить сверхзвуковое течение по отношению к этой аномально низкой скорости звука. Итак, на выходе из КС мы можем с малыми энергозатратами получить сверхзвуковую скорость. Затем сверхзвуковой поток переходит из КС в ГД (рис.2), т.е. в канал постоянного сечения. Учитывая, что скорость смеси достаточно велика при относительно небольшой длине канала, то процесс, происходящий в нем можно считать адиабатным.
При торможении потока в адиабатном канале, согласно формуле Эддингтона, из работы [6], для газожидкостной смеси интенсивность скачка давления равна числу Маха в квадрате Р2/Р1= М2, где Р1 и Р2 — соответственно давления до и после скачка. Число Маха дает отношение скорости потока W к скорости звука в потоке. С: М = W / C Так, если W= 50 м/с, С=10м/с, то М=50/10=5, тогда Р1 / Р2 = 52 = 25, т.е. имеем двадцатипятикратный (!) скачок давления. С учетом падения давления пара в сопле и перед скачком давления смеси, все равно давление после скачка может существенно превышать его значение на входах в аппарат. Как показали визуальные наблюдения, выполненные на аппаратах с КС и ГД из кварцевого стекла, за скачком поток имеет однородную структуру (жидкость практически лишена паровых пузырьков и поэтому оптически прозрачна), т.е. переход через скорость звука сопровождается скачком давления с “захлопыванием” пузырьков и полной конденсацией пара. Статическое давление по длине аппарата ведет себя следующим образом:
I — на этом участке давление падает в паровом и жидкостном соплах; II — на срезе сопла давление примерно равно давлению в КС, если сопло работает в расчетном режиме. Давление в КС по завершению формирования смеси устанавливается равным давлению насыщения при температуре на границе раздела фаз, в зависимости от требуемой температуры смеси оно может быть больше или меньше атмосферного; III — давление в начале ГД падает перед скачком, т.к. сконденсировавшийся пар занимает меньший удельный объем, чем до конденсации, а сечение цилиндрического участка постоянно в отличии от КС ; IV — дозвуковое течение смеси. На границе участков III и IV происходит скачок давления, его рост продолжается в диффузоре. Рраз — разряжение в ГД, Р- превышение давления смеси на выходе из аппарата над давлением пара на входе.
4. Рабочая характеристика.
Рассмотрим зависимость расхода смеси Gс на выходе из аппарата и ее температуры Тс от противодавления Рс, оказываемое системой. Параметры потоков на входе в аппарат будем считать фиксированными. Так для аппарата с центральным подводом пара и периферийным подводом жидкости входными параметрами являются: Рр — давление рабочего потока (пара), Тр — его температура (для перегретого пара), Рн — давление инжектируемого потока (воды), Тн — его температура. То есть рассмотрим функции Gс= Gc (Pc), Tc = Tc (Pc) При любой внутренней геометрии и значений входных параметров, для используемых нами аппаратов работающих без срыва, эти зависимости имеют качественно следующий вид (рис. 6).
|
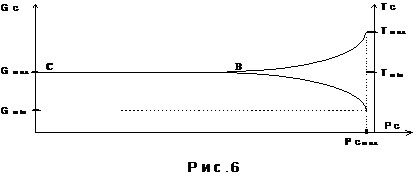
|
|
Из этого графика следует, что при изменении противодавления от нуля до некоторого значения мы имеем на выходе из аппарата неизменный расход равный максимальному значению, а температура имеет постоянное минимальное значение (участок СВ на графике). Затем дальнейшее возрастание противодавления приводит к уменьшению расхода смеси через аппарат с одновременным повышением температуры смеси на его выходе. Наконец, при значении противодавления, превышающем Рсmax наступает срыв работы аппарата. Этому максимально допустимому значению противодавления, для работы без срыва, соответствует минимальный расход жидкости Gmin на выходе из аппарата и ее максимальная температура Tmax. Участок СВ графика соответствует сверхзвуковому режиму работы, так как изменение противодавления не оказывает влияния на работу аппарата: расход и температура нагретой воды на выходе не изменяется. Область правее точки В дает выход аппарата из сверхзвукового режима в дозвуковой, так как параметры потока изменяются с изменением противодавления. Наша методика расчета геометрии аппарата основывается на том, что противодавление, закладываемое в расчет, должно соответствовать одной из точек на участке СВ рабочей характеристики. Это определяется тем, что сверхзвуковой режим работы аппарата является наиболее устойчивым по отношению к колебанию входных параметров и изменению противодавления на выходе. Сверхзвуковой режим работы на отрезке СВ соответствует постоянному коэффициенту инжекции u = Gн/Gр. Для традиционных пароводяных инжекторов, которым соответствует область правее точки В на рабочей характеристике, коэффициент инжекции имеет переменное значение.
5.Выводы.
Данный аппарат идеально подходит для технологических процессов, где надо перемешать, нагреть и прокачать различные смеси жидких и газовых сред.
Способность аппарата преобразовывать тепловую и механическую энергию пара и жидкости на входе в аппарат в тепловую и потенциальную энергию давления смеси на выходе, практически без потерь тепловой энергии, делает актуальным применение аппарата для систем горячего водоснабжения и отопления, с целью замены традиционных теплообменников. А также для частичной или полной замены циркуляционных насосов и для использования в качестве эмульгаторов, диспергаторов, экстракторов.
Литература:
[1] М.Е. Дейч Г.А. Филиппов Газодинамика двухфазных сред. М.: Энергоиздат, 1981. [2] В.И. Коновалов Некоторые вопросы теории инжектора и струйного подогревателя. / Изв. ВТИ. 1951. №5. [3] Л.Д. Ландау, Е.М. Лифшиц. Механика сплошных сред. 1963. [4] В.В. Сычев. ИФЖ № 6, 1961. [5] Н.И. Семенов, С.И. Костерин. Теплоэнергетика № 6, 1964. [6] Р.Б. Эддингтон Изучение сверхзвуковых явлений в двухфазной (газожидкосной) аэродинамической трубе. / Ракетная техника и космонавтика, 1970, т. 8 №1.
|